Our experienced die designers and forging engineers work together with our customers to determine the best design required to cost-effectively produce a specific part.
For longer than 30 years, Wyman-Gordon Cleveland has been manufacturing standard and custom metal closed die forging products for the Aerospace, Commercial, Medical, Transportation and Ordnance industries.
We know quality, time, and value are our customers' primary concerns. That's why we use only the most innovative CNC-programmable machines. Our investment in PLC logic provides increased flexibility and process control which translate into greater overall quality.
Quality Assurance is the highest priority at Wyman-Gordon. Each part goes through rigorous inspections before, during, and after production to ensure the part is exactly as the customer ordered.
History
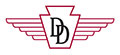
Drop Dies and ForgingsFounded in 1919 by Joseph F. Rice, the former Drop Dies and Forgings Company was in its third generation of family leadership when it was acquired by Wyman-Gordon, parent company, Precision Castparts Corp., in December 2000.
With customer satisfaction at the foundation of the entire operation, Wyman-Gordon Forgings (Cleveland), Inc. is dedicated to maintaining the Drop Dies and Forging Company's commitment to providing the highest quality products, the best customer service, and the safest operating conditions in the industry.
Aerospace
- Fuel Nozzles
- Engine Components
- Valves & Fittings
- Structural Components
Commercial
- Hardware
- Valves & Fittings
Medical
- Implants
- Instruments
Automotive Specialty
- Aircraft & Helicopter Components
Ordnance
- Aircraft & Helicopter Components
Other
- Diesel Fuel Systems Components
- Various Other Industrial Products
Equipment
Wyman-Gordon produces high intensity forgings for some of the most technically challenging and demanding applications in the world.
- Forge Hammer: 1,000 – 3,000 lbs
- Mechanical Press: 1,000 – 2,500 Tons
- Screw Press: up to 1,600 Tons
- 2D Matrix Part Making
- Coining Press: 75 – 750 Tons
- Extrusion Press: 400 – 440 Tons
- CNC Machines
- White Light Scanner
- Upset & Extrusion Capabilities
- Closed-Die Presses: up to 50K Tons
- Ultrasonic Tanks
- Flow Detectors
Tool & Die Making
- In-House Manufacturing
- High Speed Direct Mill
- CNC
- EDM
Materials
Wyman-Gordon manufactures forged components from high grade titanium and nickel based alloys.
Stainless Steel
- 300 & 400 Series
- 17-4-PH
- 15-5-PH
- PH13-8MO
- 21-6-9
Titanium Alloys
- CP
- 6AL-4V
- 4965
High Temperature Alloys
- Hastelloy*
- Waspaloy**
- A-286
Nickel Alloys
- Inconel 600
- Inconel 625
- Inconel 718
- Monel 400
- Monel 500
Aluminum Alloys
- 2014
- 6061
- 7075
Cobalt-Chrome
- Medical Grade
Carbon & Alloy Steels
- All Grades
Zirconium
*Hastelloy is a registered Trademark of Cabot Corp.
**Waspaloy is a registered Trademark of Union Technologies Corp.
Quality Systems
- ISO 9001:2015/AS9100 Rev. D
- Nadcap Accredited for FPI
- Pressure Equipment Directive 2014/68/EU
- NORSOK Standards
- Standards
- NCA - 3800
- MIL-I-45208
- ISO 10012-1 (MIL-STD-45662)
- ASTM-E1444 (MIL-STD-1949)
- P3TF2
Quality Programs
- General Electric Aircraft Engines
- Pratt & Whitney LCS
- Cessna
- Parker Hannifin Corp
- Eaton Corp
- Swagelok
- Rolls Royce
Speaking the Common Language
It is our desire to communicate and exchange information as easily and quickly as possible with our partners in business. We have assembled the following information to asst with making the exchange process simple and efficient.
For questions regarding CAD file exchange please call us at 216-341-0085, ext. 141.
CAD File Exchange
Our Software:
- 2D/3D Surface Modeling Capable
File Type:
- 2D Files: DXF or IGES files
- 3D Wireframe: IGES files
- Surface or solid models: IGES files
Particulars:
- Media: 3.5 inch floppy disks, CD or email
Along with only the highest quality materials and the most efficient forging processes, our parts are continually monitored for dimensional accuracy and thoroughly checked for structural integrity to aerospace, military, and customer specifications.
Using advanced tools such as Coordinate Measuring Machine (CMM) and an Optical Comparator, Wyman-Gordon measures and confirms geometric tolerances such as length, height, diameter, and radius, before, during, and after the production process.
Quality assurance is paramount ot the success of our business. Before a part is shipped and delivered, all procedures and customer specifications are documented and certified. This ensures the prescribed processes were performed and correctly completed. Our in-house metallurgical lab provides better control over lead times and delivery, while cutting costs at the same time. To maintain consistent workmanship, vendors performing processes, such as heat treatment and chemical cleaning, are audited on a regular basis.
Fluorescent penetrant inspection is performed to required specifications. The latest equipment is used to perform microstructural analysis such as measuring gram size.