Wyman-Gordon's North Grafton, Massachusetts, forging facility is a trusted supplier of highly-engineered, closed and open-die titanium, steel and nickel-based forgings.
Our diverse capabilities fulfill the critical requirements of aerospace, energy, and military OEMs globally.
With some of the largest and most capable forging equipment in the world, combined with modern design, modeling and simulation capabilities, provide timely, creative, and high-quality solutions to the most difficult manufacturing challenges.
Wyman-Gordon's North Grafton facility is part of the family of Wyman-Gordon forging facilities across North America and the UK. Together, the complementary capabilities of each provide the full spectrum of forging, capabilities and options for customer requirements.
History
Originally founded in 1883 in Worcester, MA, the Wyman-Gordon Company boasts more than 125 years of forging experience and first manufactured forgings for the aerospace industry during WWI.
Recognizing the need for more expansive heavy manufacturing capabilities to support larger and more advanced aircraft designs, the Department of Defense built the forging facility now located in North Grafton, MA in 1946, equipping it initially with an 18,000 ton closed-die press.
In 1953, the facility was expanded to include the 35,000 and 50,000 ton presses in what was referred to as the “Air Force Heavy Press Program”. From this program’s inception, Wyman-Gordon was chosen to operate the North Grafton facility due to the company’s long-term experience and reputation in the industry.
In 1988, Wyman-Gordon purchased the facility outright from the U.S. Government and ran it as a private company until 1999 when Wyman-Gordon was acquired by Precision Castparts Corp. (PCC).
Commercial Aerospace Applications
Forged Airframe Structures
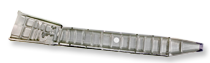
Wide-Body Wing Beam
(5,000lbs Ti 6-4)
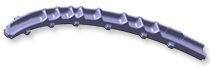
Wide-Body Door Frame (400lbs Ti 6-4)
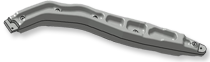
Narrow-Body Flap Track
(600lbs 15-5)
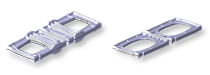
Wide-Body Engine Pylon Ribs
(500lbs Ti 6-4)
Forged Landing Gear
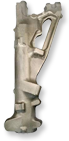
Wide-Body MLG
(14,000lbs 300M)
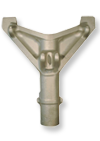
Wide-Body NLG
(2,700lbs 300M)
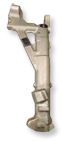
Narrow-Body MLG
(4,200lbs E35NCD16)
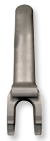
Wide-Body MLG Piston
(5,000lbs 300M)
Forged Engine Components
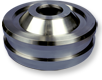
Engine Fan Disk
(1,300lbs Ti-17)
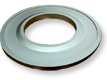
LPT Disk
(1,200lbs Inco-718)
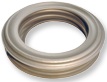
LPT Disk
(1,500lbs Inco-718)
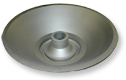
LPT Cone Shaft
(10,000lbs Inco-706)
Military Aerospace Applications
Forged Airframe Structures
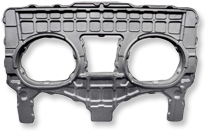
Fighter Fuselage Bulkhead
(3,000lbs Ti 6-4)
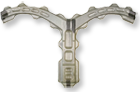
Fighter Fuselage Bulkhead
(1,000lbs Ti 6-4)
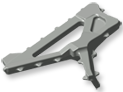
Transport Flap Hinge
(900lbs Ti 6-4)
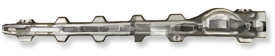
Fighter Frame
(500lbs Ti 6-4 Eli)
Forged Landing Gear
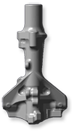
Fighter NLG
(1,000lbs Aermet 100)
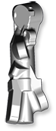
Fighter MLG
(600lbs Aermet 100)
Forged Rotor Components
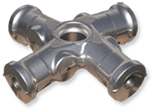
Helicopter Main Rotor Hub
(800lbs Ti 6-4)
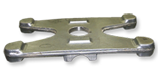
Helicopter Rotor Yoke
(200lbs Ti 6-4 DM)
Energy Applications
Industrial Gas Turbine Products
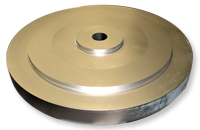
IGT Turbine Disk
(10,000lbs Inco-706)
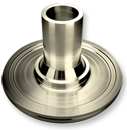
IGT Turbine Shaft
(12,000lbs Inco-706)
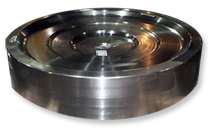
IGT Spacer
(20,000lbs Inco-706)
Nuclear Products
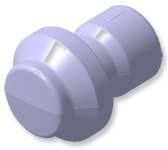
Bonnet
(1,500lbs Inco-600)
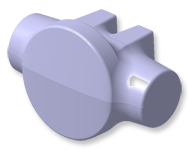
Value
(1,800lbs Inco-600)
Oil & Gas Refining
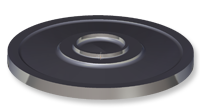
Turbine Wheel
(4,000lbs Inco-901)
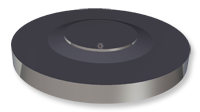
Value
(6,000lbs Waspalloy)
Forgings for Naval Vessels
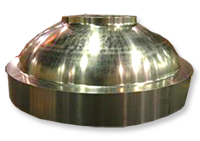
Submarine Component
(2,000lbs CP Ti)
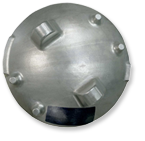
Submarine Component
(300lbs CP Ti)
Forgings Compliant with MIL Spec:
MIL-DTL-46077
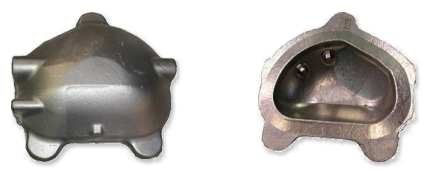
Armored Hatch (Production Vehicle)
(250lbs 6-4 Ti)
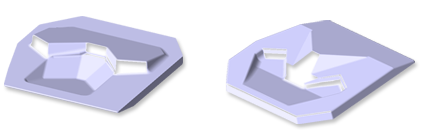
Armored Hatch (Developmental Vehicle)
(300lbs 6-4 Ti)
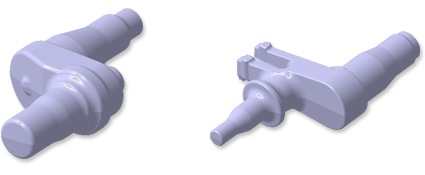
Suspension Idler Arms (Tracked Vehicles)
(350lbs 4340)
Equipment
18,000 Ton Closed-Die Press
35,000 Ton Closed-Die Press
50,000 Ton Closed-Die Press
Forgings
- 100 pounds to 15,000 pounds
- Presses from 2,000 to 50,000 tons
- Raw Material Conversion
- Heat Treatment
- Forging Machining: Rough and Target Machining
- Die Machining: New Die Sinking, Existing die modification and refurbishment
- NDT: Sonic Inspection, Penetrant Inspection, Magnetic Inspection
- Chemical Etching and Milling
- 3D Forging Surface Scanning
Materials
- Titanium
- Nickel-Based Alloys
Plant Size
- 1,050,000 Sq Feet
- 97,550 Sq Meters
Engineering
Wyman-Gordon provides full engineering services from collaborative concept development for developmental programs, to full design, modeling and simulation of production-ready forging products. 3-dimensional design of forgings and associated tooling uses CATIA V4/5. Proposed processes are simulated and refined with FEA (Finite Element Analysis) modeling techniques, and tool stress is analyzed and corrected prior to manufacture.
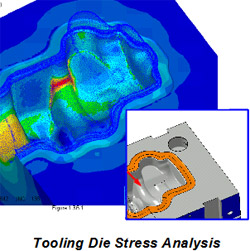
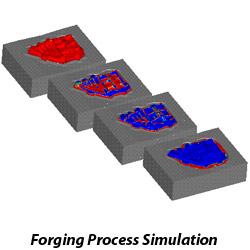
3D Design and Simulation
Modern design and simulation capabilities compatible with OEMs.
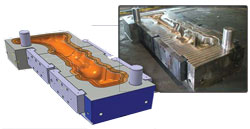
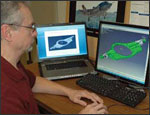
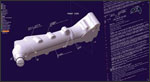