Wyman-Gordon’s Livingston facility, located in Scotland, UK, supplies forged products globally to the aerospace and energy markets.
It has a unique 30,000 ton Hydraulic multi ram closed-die press at the heart of the operation, which is supported by Heat Treatment, Material Handling, Die & Tool Machining and Non-Destructive Testing & Inspection facilities.
The 30,000 ton press is capable of multi-directional piercing and hot die forging of Aerospace, Powergen, Oil & Gas and Nuclear components (asymmetric forgings, discs, seamless extruded pipe, valve bodies and hollow forged T’s). It is the largest of its type in Europe, forging at temperatures of up to 1200°c. The 9,000 ton pre-forming press prepares the billet for the closed die forging process, ensuring a continuous smooth operation. CNC technology ensures repeatability throughout the entire forging operation.
History
Cameron Iron Works was co-founded in Houston, Texas in 1921, by two Scots-Americans, Harry Cameron and Jim Abercrombie. In 1964, they established a Forging operation in Livingston serving the UK and European market. The site cost £12M ($18M) to build and equip becoming fully operational in 1966. The unique 30,000 ton press was installed at this time.
Cooper Industries purchased Cameron Iron Works in 1991 and split the business, transferring a portion of the business to France. In 1994, Wyman-Gordon purchased the strongly performing Forged Products Division in Livingston. At the end of 1999, Wyman-Gordon was acquired by Precision Castparts Corporation.
Today, the Livingston Facility works in unison with sister plants in Lincoln, UK, and Plzen, Czech Republic, to provide a diverse range of machined forgings serving customers globally.
Reports
Gender Pay Gap Report | Rev. Apr 2020 |
Retirement Plan Statement of Investment Principles | Rev. Dec 2023 |
Annual Implementation Statement | Rev. July 2023 |
Products
Manufacture of Compressor, Turbine & Fan Discs.
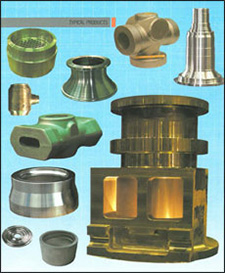
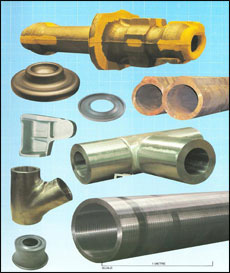
Aerospace Applications
Forged Engine Components
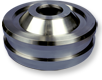
Engine Fan Disk
1,300lbs Ti-17
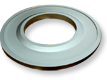
LPT Disk
1,200lbs Inco-718
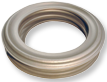
LPT Disk
1,500lbs Inco-718
Energy Applications
Industrial Gas Turbine Products
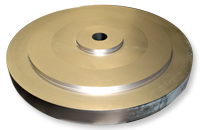
IGT Turbine Disk
(10,000lbs)
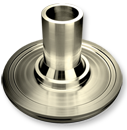
IGT Turbine Disk
(12,000lbs Inco-706)
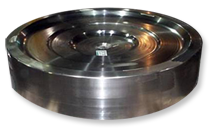
IGT Spacer
(20,000lbs Inco-706)
Valve Products
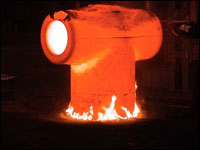
Valve Bodies
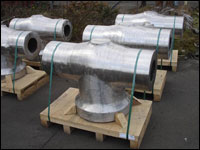
Valve Products
Oil & Gas Refining
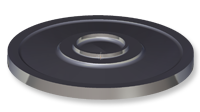
Turbine Wheel
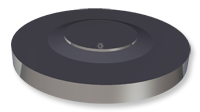
Compressor Disk
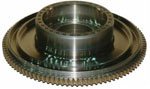
Oil & Gas
Seamless Pipes
Duplex and super Duplex extruded pipe for offshore applications Extruded P91 / P22 for 300MW Power Station High Pressure Pipe Applications
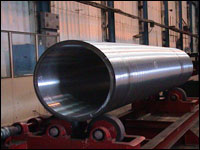
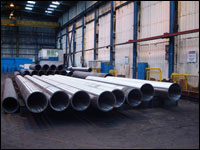
Equipment
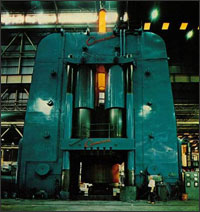
30,000 Ton Closed-Die Press
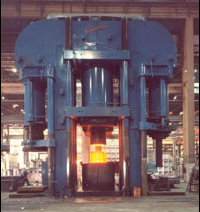
9,000 Ton Closed-Die Press
Forgings
- Die & Tool Machining: New Die Sinking, Existing Die Modification and Refurbishment
- NDT Inspection Facilities: Etch Inspection, Penetrant Inspection, Magnetic Particle Inspection
- Forging Machining: Rough Machining, UT Inspection
- Outer and Internal Diameter Grinding for Pipe Products
- Closed-Die Forging 50 - 5,000lbs
- Extruded Pipe and Powder Billet
- 30,000 and 9,000 Ton Press
- Precision Heat Treatment
- Material Handling
- Chemical Etching
Materials
- Titanium
- Nickel-Based Alloys
- Steel Alloys
Plant Size
- 800,000 Sq Feet
- 74,320 Sq Meters
Certifications
- ISO 9001
- TUV Approvals for pipe applications
- HAF for Chinese nuclear pipe applications
- PRI-NADCAP special approvals for heat treat, penetrant & chemical processing & Mag particle inspection
Engineering
- Heat Treatment Modeling Techniques
- Forge 2 & Q Form 2D & 3D - Full forging and tool design simulation
- Pro-Engineer for CAD and CNC Programming
Forging & Manufacturing
The 30,000 ton press, with two 5,000 ton side rams and a 6,000 ton piercing needle, is capable of multi-directional piercing and hot die forging of Aerospace, Powergen, Oil & Gas and Nuclear components (asymmetric forgings, discs, seamless extruded pipe, valve bodies and hollow forged T’s). It is the largest of its type in Europe, forging at temperatures up to 1200°c.
A 3 station 9,000 Ton pre-forming press prepares the billet for the closed die forging process and ensures a continuous smooth operation. The entire forging operation is process controlled using CNC technology to ensure repeatability.