Wyman-Gordon’s Lincoln facility, located in England, UK, supplies forged products globally to the aerospace and energy markets.
The DG90 hammer is capable of manufacturing hot die forging of Aerospace, Powergen, Oil & Gas and Nuclear components (asymmetric forgings, discs, shafts and valve bodies). It is the largest of its type in Europe, forging at temperatures of up to 1340°c.
Smaller components are manufactured on the 400KJ DG40 counterblow hammer. Both counterblow hammers are full computer controlled to ensure repeatability of the process. The 2 counterblow hammers are supported by a Zdas 630T CNC controlled pull down press which is utilized in the manufacture of pre-forms for asymmetric structural parts and long aero engine shafts.
History
Smith-Clayton Forge was established in 1929 in Lincoln for the manufacture of aerospace and automotive forged products for a cost of £50,000. In 1956 the DG40, the first of the 2 counterblow hammers was installed, followed by the DG80 in 1970. The DG80 being uprated to DG90 in 2008.
In May 2000 the Aerospace Division of what was then known as UEF was acquired by Precision Castparts Corporation and incorporated into the Wyman-Gordon Forging Division.
Today, the Lincoln Facility works in unison with sister plants in Livingston, UK, and Plzen, Czech Republic, to provide a diverse range of machined forgings serving customers globally.
Products
Manufacture of Compressor, Turbine & Fan Disks, valve bodies, and shafts.
Aerospace Applications
Forged Engine Components
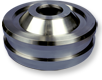
Engine Fan Disk
1,300lbs Ti-17
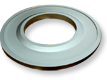
LPT Disk
1,200lbs Inco-718
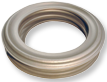
LPT Disk
1,500lbs Inco-718
Energy Applications
Industrial Gas Turbine Products
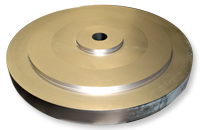
IGT Turbine Disk
(10,000lbs)
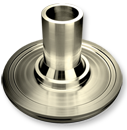
IGT Turbine Disk
(12,000lbs Inco-706)
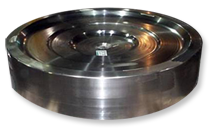
IGT Spacer
(20,000lbs Inco-706)
Equipment
DG90 Computerized Counterblow Hammer
630T CNC Controlled Pull Down Press
Forgings
- Closed-Die Forging 10lbs - 2000lbs
- A 900KJ and 400KJ computerized counterblow hammers
- 630T CNC controlled pull down press
- Material Handling
- Die & Tool Machining: New Die Sinking, Existing Die Modification and Refurbishment
- NDT Inspection Facilities: Etch Inspection, Penetrant Inspection, Magnetic Particle Inspection
- Forging Machining: Rough Machining
- Precision Heat Treatment, including vertical heat treatment and quenching for long shafts
Materials
- Titanium
- Nickel-Based Alloys
- Steel Alloys
Plant Size
- 190,000 Sq Feet
- 17,600 Sq Meters
Quality Certifications
- ISO 9001
- AS 9100
- PRI-NADCAP special process approvals for heat treat, penetrant & chemical processing & Mag particle inspection
Engineering
- Heat Treatment modeling techniques
- Q Form 2D & 3D - Full forging and tool design simulation
- Pro-Engineer for CAD and CNC Programming
Forging & Manufacturing
The 900KJ and 400KJ hammers are both utilized to manufacture closed-die forgings for aero engine, IGT and airframe markets worldwide. In addition, specialist industrial, nuclear, and automotive products such as large connecting rods and valve bodies are also forged. The Zdas 630T pull down press is utilized to forge long aero engine shafts and asymmetric preforms for subsequent closed-die forging on the counterblow hammers.